When it comes to eyewear, whether corrective glasses or sunglasses, the most vital component is undoubtedly the lens. Among the various lens materials available today, CR39 lenses stand out as one of the most widely used options. This article delves into the significance of CR39 lenses, exploring their characteristics, manufacturing processes, and applications in contemporary eyewear.
Understanding CR39 Lenses
CR39 lenses, also known as Columbia Resin #39, are a type of thermosetting polymer developed in 1942 by the PPG Industries’ Columbia Laboratory in the United States. Initially designed for use in aircraft canopies, CR39 lenses have since become a staple in both corrective and sun lenses due to their excellent optical properties and durability. Today, CR39 lenses are prevalent in various types of sunglasses, particularly in high-end acetate and metal frames.
Key Characteristics of CR39 Lenses
Among the most common lens materials—CR39 lenses, nylon, and polycarbonate (PC)—CR39 lenses offer several advantages:
- High Light Transmission: CR39 lenses allow a significant amount of light to pass through, ensuring clear and vibrant vision.
- Durability: With a high hardness level, CR39 lenses are more resistant to scratches and impacts compared to other resin lenses.
- Lightweight: CR39 lenses strike a balance between strength and weight, making them comfortable for prolonged wear.
- Color Variety: CR39 lenses are available in a wide range of colors, enhancing both functionality and aesthetic appeal.
These attributes make CR39 lenses a favorite choice among consumers, especially for fashionable acetate and metal eyewear.
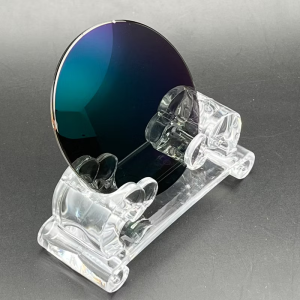
Manufacturing Process of CR39 Lenses
The production of CR39 lenses involves several meticulous steps to ensure quality and precision:
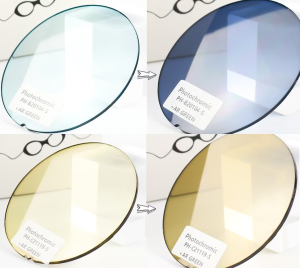
- Mold Preparation: The first step involves creating molds with specific dimensions, curvatures, and thicknesses tailored to different lens specifications.
- Casting: CR39 resin material is cast into these molds using a compression molding technique, resulting in the formation of CR39 blanks.
- Coloring: After molding, the CR39 blanks undergo a dyeing process. This can produce single-colored lenses (such as gray, green, brown, yellow, or red) or gradient lenses (like gradient gray, green, or brown). Additionally, lenses can be custom-colored based on customer requirements.
- Coating: Various coatings are applied to enhance functionality and aesthetics:
- Mirrored Coatings: Applied using vacuum deposition, these coatings can be gold, silver, blue, green, pink, or orange, adding a reflective surface to the lenses.
- Back Coatings: A layer is added to the backside of the lens to reduce light reflection and improve privacy by making the lenses less visible from the outside.
- UV400 Protection: UV400 particles are incorporated into the resin to filter out harmful ultraviolet rays, resulting in lenses with a slight yellow tint. This is a standard feature in most mid-to-high-end sunglasses.
- Strengthening: Although CR39 lenses are harder than nylon and PC, additional strengthening treatments are often applied to enhance durability. Strengthened lenses exhibit a glossy appearance on the sides, unlike the matte finish of untreated CR39 lenses.
- Hydrophobic and Oleophobic Coatings: These treatments repel water and oil, respectively, improving lens maintenance and longevity. The effectiveness of these coatings can be tested by observing water droplet behavior or the removal of oil-based marks.
Identifying CR39 Lenses
Distinguishing CR39 lenses from other materials like nylon and PC can be achieved through several methods:
- Knife Scratch Test: Gently scratching the lens’s edge with a utility knife. CR39 lenses will produce a powdery residue, whereas nylon and PC will show fibrous strands.
- Shape Inspection: CR39 lenses typically lack a handle or stem, which is common in nylon and PC lenses.
- Sound Test: Tapping the lens lightly can help identify the material based on the sound produced. CR39 lenses emit a deeper, more resonant sound, nylon sounds brittle, and PC is the most high-pitched and crisp.
Discover Custom CR39 Lenses at Eyefiy
We understand that finding the right eyewear is a personal journey. Whether you’re looking for high-quality CR39 lenses or frames that perfectly match your style, we’re here to help. Our custom services are designed to work with you, ensuring your glasses are comfortable, durable, and stylish.
Applications of CR39 Lenses
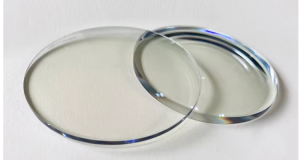
CR39 lenses are versatile and widely used in various eyewear styles:
- Corrective Glasses: Most prescription lenses today are made from CR39 lenses due to their excellent optical clarity and comfort.
- Sunglasses: CR39 lenses are a popular choice for different types of sunglasses, including acetate, metal, titanium, and buffalo horn frames. However, irregularly shaped frames with sharp edges may not be suitable for CR39 lenses.
- Fashion Eyewear: The ability to color and coat CR39 lenses makes them ideal for trendy and designer eyewear, catering to diverse consumer preferences.
Conclusion
CR39 lenses have cemented their place as a cornerstone in the eyewear industry, thanks to their superior optical properties, durability, and versatility. Whether in high-end sunglasses or everyday corrective glasses, CR39 lenses continue to meet the demands of both manufacturers and consumers. As technology advances, CR39 lenses remain a reliable and preferred choice, ensuring clear vision and stylish protection for eyewear enthusiasts worldwide.